Best practices by another name
If you can teach an engaged community of hands-on professionals how to design out waste and extend lifecycles, do you need to tell them you’re offering a crash course in the circular economy?
This month, Heidi Frasure of Green Standards and Dean Stanberry of IFMA co-hosted a webinar for facility managers titled From Waste to Worth: Best Practices in Office Cleanouts. The subject was keeping furniture, fixtures, and equipment in use and out of landfill: the basics of workplace circularity. But in the spirit of meeting people where they are — and not introducing jargon that might seem irrelevant to the target audience — they made only passing reference to the circular economy. Because when you get right down to it in an office cleanout, circularity is just smart project management.
The best practices presented were straightforward because as usual, the devil is in the details. Here are the tips, along with the real-life factors that make them tricky to realize:
- Plan ahead. The last-minute option is always the landfill. With more lead time, donation, resale, and reuse can be explored. That means knowing when a cleanout is coming your way.
- Communicate with colleagues. Do facility managers know what’s happening in the next six months, year, or two years? Often the answer is no, and it’s worth asking why.
- Secure budget. Reuse isn’t free, but neither is the landfill. Dispel the notion that there’s no cost to disposal and unpack the long-term value of reuse.
- Think bigger. If you can make reuse work in one building, why not rinse-and-repeat across an entire portfolio?
- Report results. Better measurement leads to better management — and that can include landfill diversion and emissions avoided.
Ultimately, workplace circularity is the better way to run a business. No matter what they call it, anyone interested in that outcome can be part of the solution.
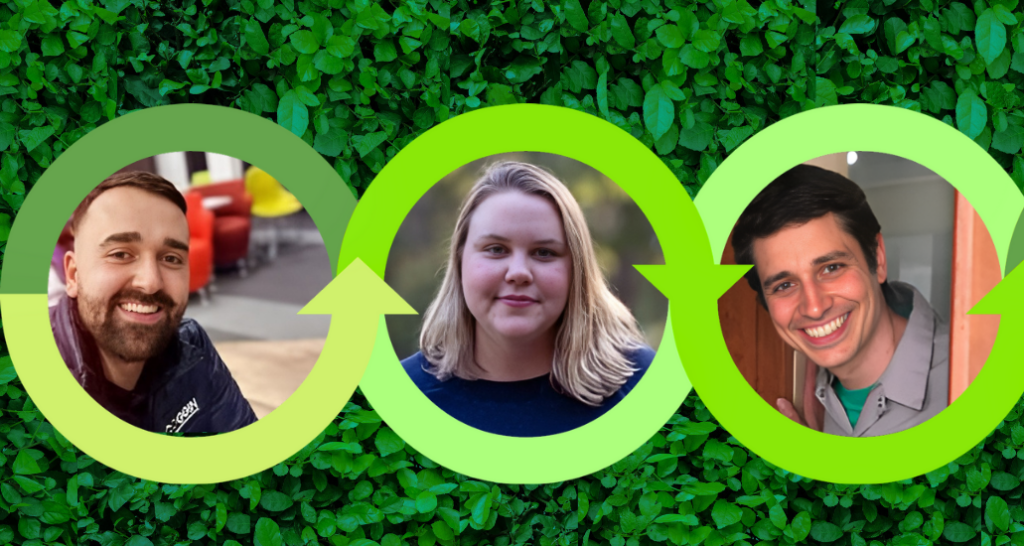
We’re always looking for new voices on workplace circularity at circularsurvey.com, and we highlight your advice for other members of the Circular Workplace coalition here each month:
For procurement teams: “Shift from a traditional linear purchasing model to a more circular approach.
1. Encourage sustainable purchasing: Prioritize sourcing refurbished, recycled, or upcycled furniture and materials over new products.
2. Develop supplier partnerships: Work with vendors who offer take-back programs or eco-friendly options, and favor suppliers who design products with durability and ease of refurbishment in mind.
3. Lifecycle costing: Train procurement teams to focus on the total lifecycle cost of a product, considering maintenance, refurbishment potential, and disposal, rather than just the initial purchase price.”
— Sam Coggin,Company Director, Coggin Sustainable Office Solutions, Lancashire, UK
For IT: “Create a system that tracks the full lifecycle of IT assets —from procurement to end-of-life. Regular audits help identify when technology can be repurposed internally, donated, or refurbished. This data-driven approach ensures no device is prematurely discarded and keeps circularity top-of-mind across the entire IT department.”
— Tori Lowe,
Manager of Business Development, Human-I-T, Los Angeles
For circularity champions: “Be flexible! Rigidity is the enemy of circularity. We need to be ready to adapt our designs to work with what’s available. Start early! Don’t wait until the last minute, it takes time and effort to maximize waste diversion and reuse of existing products. Deconstruction & salvage has no impact without reuse of those same products.”
— Andrew Ellsworth,
CEO, Doors Unhinged, Pittsburgh
Building a knowledge base for architects and designers
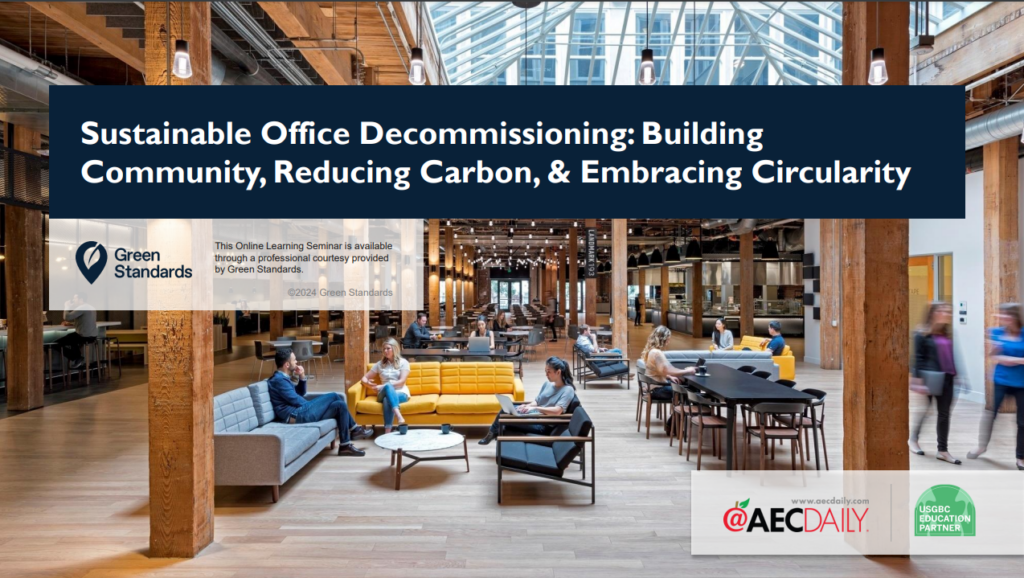
If you know that sustainable office decommissioning saves time, money, waste, carbon, and headaches, you deserve credit!
And now you can get it with Green Standards’ new free continuing education course, approved by the The American Institute of Architects, the International Design Continuing Education Council, Green Business Certification Inc., and 26 more industry associations.
Got a case study, actionable tip, or news item about the circular workplace? Reach out at hello@circularworkplace.com to join our coalition.
Signup for the Roundup
Subscribe to our newsletter and we’ll send you circular workplace updates every month
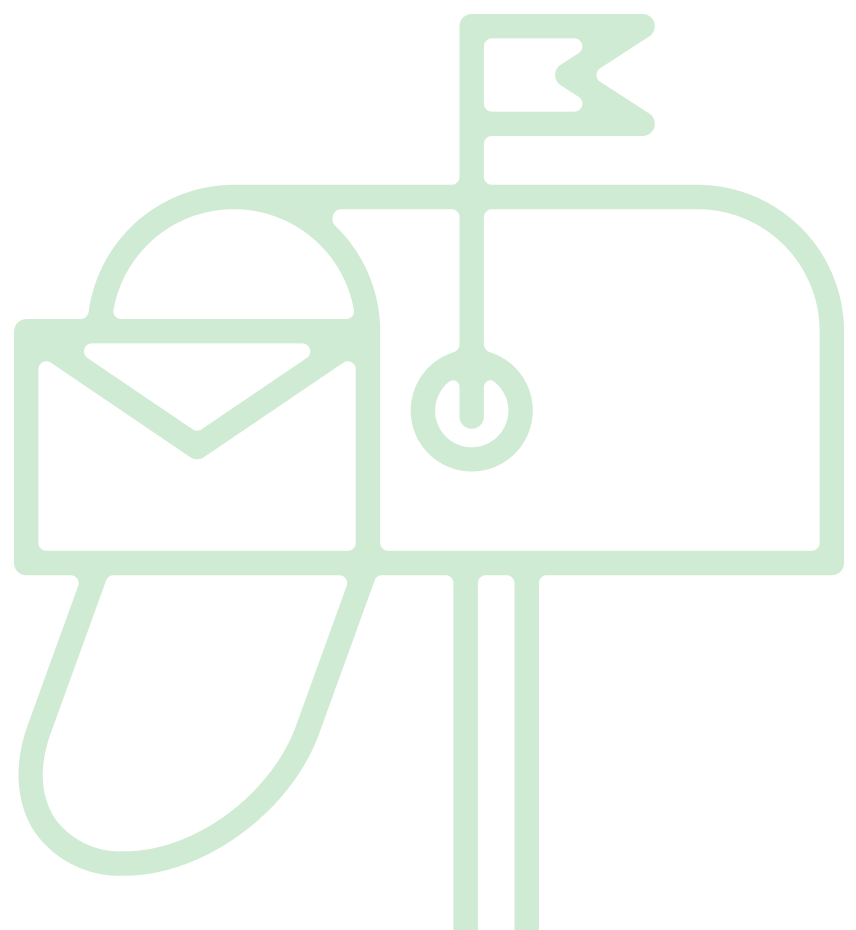